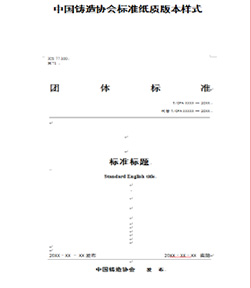
标准情况说明
目的:1、 推动技术升级与创新:通过明确工艺参数、材料性能等技术要求,引导企业突破传统压铸技术的局限性,促进大型一体化压铸技术向高精度、复杂结构方向发展; 2、 适应新能源汽车发展需求:针对新能源汽车轻量化、高续航的迫切需求,规范铝合金一体化压铸工艺,提升车身结构集成度,降低制造成本,满足行业对高效、节能技术的需求; 3、 规范行业技术门槛:统一压铸工艺中的材料选择、模具设计、后处理等关键环节的技术指标,避免因工艺标准缺失导致的质量参差不齐和资源浪费。
意义:1、 促进产业协同与升级:标准化工艺要求可减少上下游企业间的技术壁垒,推动产业链协同发展,加速从材料研发到终端应用的整合; 2、 提升国际竞争力:通过与国际主流标准接轨,改变依赖国外牌号和技术规范的现状,增强我国在压铸铝合金领域的技术话语权; 3、 保障产品质量与安全性:通过标准化控制熔融温度、压射参数等核心工艺,减少铸件缺陷(如气孔、裂纹),确保产品力学性能和结构可靠性; 4、 助力绿色制造与可持续发展:优化材料利用率,降低生产能耗,符合国家节能减排政策导向; 5、 降低综合成本:通过工艺标准化减少试错成本,缩短生产周期,同时降低后期维修和维护成本,提升企业经济效益。
必要性:新能源汽车渗透率已达31.6%,2030年目标超50%,单车用铝量预计从2023年250kg增至2030年350kg,轻量化材料需求迫切,一体化压铸技术可整合300+零部件,实现车身减重17%、刚度提升30%,显著降低能耗与制造成本(降本40%)。压铸件应用从传统动力总成(缸体、变速器壳体)向车身结构件(电池包壳体、底盘横梁)扩展,覆盖汽车制造全流程。现有工艺存在裂纹、冷隔、缩陷等缺陷(如龟裂纹发生率超15%),需通过标准化参数优化模温、浇道设计及压射比压(建议提升至90MPa以上),免热处理铝合金材料、超大型压铸设备(≥6000T锁模力)缺乏统一技术指标,导致产品性能差异显著(强度波动范围达20%),通过制定铝合金一体化压铸工艺技术标准,可系统性解决行业痛点,推动技术迭代与产业升级,支撑新能源汽车轻量化战略目标实现
本标准规定了:铝合金一体化压铸用材料、压铸模具设计与制造、生产设备等的要求,以及生产场地、压铸工艺和铸件检验与控制的要求。
本标准适用于: 铝合金一体化压铸工艺的生产、检验和控制。
1.国内外对该技术研究情况说明:国外技术研究进展:特斯拉率先实现产业化突破,2019年提出多向一体压铸专利,通过四向移动模具协同成型技术实现车身结构件一体化制造,显著减少零部件数量与焊点。2020年与意大利IDRA合作推出9000T压铸机,推动后地板等大型结构件量产;欧洲布勒集团开发真空压铸与高精度模温控制技术(±1℃),解决气孔率问题(气孔率<0.5%),提升铸件力学性能(抗拉强度≥300MPa)。美国铝业(Alcoa)研发免热处理铝合金AA6111,通过微合金化(添加Mn、Sr)改善流动性,延伸率提升至12%以上,已用于特斯拉Model Y后地板量产。德国Simulor压铸仿真系统实现工艺参数动态优化,良品率提升至95%以上,推动宝马、奔驰等车企布局前舱总成一体化压铸。 国内技术研究进展:力劲科技推出全球首台12000T超大型压铸机,支持1.8m×1.5m车身底板一体化成型,良品率突破90%,已应用于小鹏G6等车型。海天金属开发智能压铸岛系统,集成AI视觉检测与实时压力反馈,单件生产周期缩短至100秒,能耗降低20%。立中集团开发免热处理Al-Mg-Si-Cu合金(抗拉强度≥260MPa,延伸率≥10%),解决热处理变形问题,良品率提升至95%以上,获蔚来ET5等车型批量采用,上海交大联合文灿股份攻关高强韧压铸铝合金(屈服强度≥180MPa),通过纳米析出相强化技术突破传统压铸件性能瓶颈。广汽研究院试制团队完成一体化后地板白车身试制,通过SPR(自冲铆接)与铝点焊技术优化,连接点合格率提升至95%,支撑传祺等自主品牌量产。宁德时代联合压铸企业开发电池包壳体一体化压铸技术,集成液冷板与防撞结构,减重25%,制造成本降低30%。
2.与国内相关标准间的关系:现行标准(如GB/T 15115-2020《压铸铝合金》)对传统压铸件的抗拉强度(≥280MPa)和延伸率(≥3.5%)提出要求,但未覆盖免热处理铝合金的性能指标,国际标准(如ASTM B85)则对新能源汽车用铝合金压铸件的抗拉强度(≥310MPa)和耐高温性(≥150℃)提出更高要求。体化压铸需采用免热处理铝合金(如Al-Mg-Si-Cu系合金),要求抗拉强度(230~280 MPa)、延伸率≥10%,填补国内标准空白。GB/T 25745-2010《压铸工艺规范》未明确超大型压铸件(≥1.5m)的真空压铸等技术参数。
3.相关国际标准或国外先进标准情况:欧盟通过EN 12881规定真空压铸系统的真空度(≤50mbar)和抽气速率(≥200m³/h),确保复杂型腔填充时气孔率低于0.5%。美国SAE AMS 2772标准要求真空压铸设备集成实时压力反馈系统,实现压射速度动态调整(误差≤±2%),提升大型铸件良品率。德国VDI 3409标准定义模温控制精度(±1℃)和冷却速率(≤10℃/s),适配超大型压铸件的模温梯度管理需求,减少热应力变形。日本JIS B 6601提出压铸机锁模力与铸件投影面积的匹配公式(锁模力≥1.5倍注射压力),保障一体化压铸过程稳定性。
4.对相关国际标准或国外先进标准采用程度的考虑:本文件没有采用国际标准和国外先进标准项目。
起草阶段:2025年3月~2025年5月
征求意见阶段:2025年6月~2025年9月
审查阶段:2025年10月~2025年12月
报批阶段:2026年1月~2026年3月
- 起草单位:重庆美利信科技股份有限公司
- 起草单位:广东鸿图、中信戴卡